Ladle Slag Detection Systems
Ladle Slag Detection Systems
Improve Yield and Produce Higher-Quality Steel with Ladle Slag Detection Systems
Slag carryover from ladle to tundish is a significant problem for steelmakers. Slag has a negative effect on the quality and efficiency of steelmaking, and slag infiltration is a frequent cause of costly breakouts. Ladle slag detection systems provide the accurate, reliable, and hands-free solution that continuous casting steelmakers need to manage slag carryover.
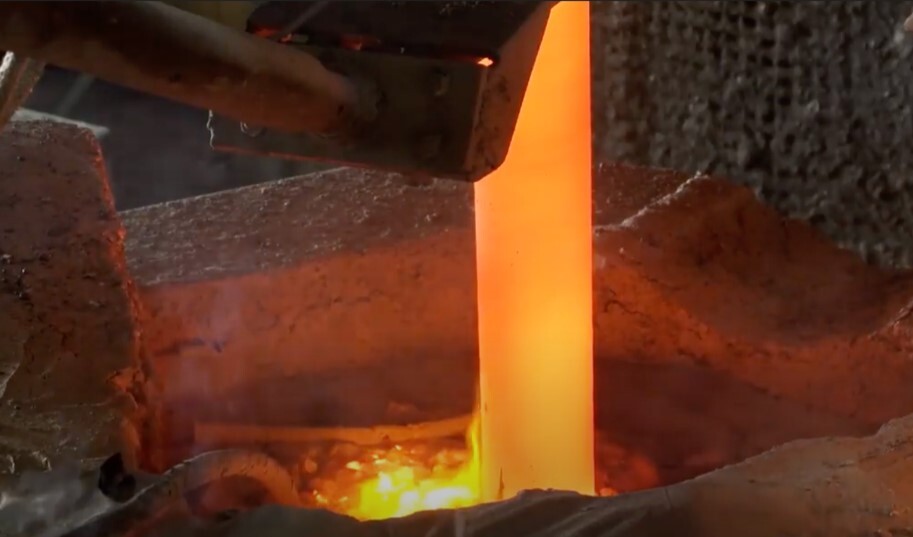
Advantages of a Ladle Slag Detection System
- Enhance steel cleanliness
- Ability to cast higher quality steel grades
- Consistently optimize yield vs. slag carryover
- Expand tundish sequence length
- Eliminate premature closing of ladles
- Reduce nozzle clogging
- Production cost savings
Interested in a high-performance ladle slag detection system?
Improve Yield and Produce Higher-Quality Steel with Ladle Slag Detection Systems
Slag carryover from ladle to tundish is a significant problem for steelmakers. Slag has a negative effect on the quality and efficiency of steelmaking, and slag infiltration is a frequent cause of costly breakouts. Ladle slag detection systems provide the accurate, reliable, and hands-free solution that continuous casting steelmakers need to manage slag carryover.
Advantages of a Ladle Slag Detection System
Mold Oscillation Issues
- Enhance steel cleanliness
- Ability to cast higher quality steel grades
- Consistently optimize yield vs. slag carryover
- Expand tundish sequence length
- Eliminate premature closing of ladles
- Reduce nozzle clogging
- Production cost savings
Interested in a high-performance ladle slag detection system?
How Kiss Technologies Can Help
Kiss Technologies has developed the industry-leading KT2000 LadleSLAG System for ladle slag detection. With over 20 years of proven performance, the KT2000 is a vibration-based system that provides consistent, reliable, and accurate management of slag from ladle to tundish. With automatic operation and adjustable sensitivity for a range of steel grades, the KT2000 will provide the optimal balance between acceptable slag carryover and steel yield for both process and economic benefit.
Key Features of the KT2000 LadleSLAG System
- Multiple sensitivity levels to accommodate the range of steel grades
- Vortex detection provides zero (0) slag carryover
- No modification to ladles, slide gates, or casting equipment
- One sensor per manipulator arm, easily installed in minutes
- Options for casters without manipulator arms
- Automatic gate closure option eliminates operator reaction time
- No operator intervention between heats to reconnect cables
- High-accuracy acoustic sensor with a 5+ year life expectancy
- Sensor with immunity to ambient plant vibration sources
- Responsive remote technical support
- Low-maintenance operation
- Fast, accurate installation
Economic Benefits of the KT2000 LadleSLAG System
Slag detection systems can save steelmakers millions by decreasing slag carryover. When slag carryover is well-managed, steelmakers can increase both the output quality of continuous casting machines, as well as the yield of each heat. With the KT2000 slag detection system in place, a range of economic benefits are realized, including:
- Yield increase per heat
- Improved tundish lining life
- Increased length of tundish sequence
- Production cost reduction
- Short-term return on investment
Annual Maintenance Costs of the KT2000 LadleSLAG System
The maintenance costs associated with other slag detection systems often amount to tens of thousands of dollars annually due to sensor damage and repair costs. Since the KT2000 sensor is installed on the manipulator arm away from liquid steel, there is a low risk of damage, meaning virtually no annual maintenance costs. In most installations, and when properly handled, KT2000 sensors survive 5 or more years.
Performance Monitoring and Reporting via YieldANALYTICS
In addition to the KT2000 LadleSLAG System’s notable accuracy and reliability, Kiss Technologies provides detailed performance reporting through our powerful YieldANALYTICS application. With data on a heat-by-heat basis, system performance can be continually monitored and improved to increase efficiency and results. YieldANALYTICS enables easy visualization and manipulation of the data gathered by the KT2000 LadleSLAG System. The application provides a range of valuable features, including:
- Detection and steel yield performance statistics and recommendations
- On-demand heat log, detection rate, and yield statistic graphs
- Statistics by month, week, shift, or other
- System fault and error notifications
Unique Features of the KISS KT2000 LadleSLAG System
The real power of a high-performance ladle slag detection system lies in the strength of its signal processing and detection algorithms. KT2000 software utilizes AI techniques that analyze complex steel flow conditions to distinguish and determine vortex and slag events for high detection rates. Statistical analysis methods are implemented for ongoing adjustment of sensitivity tuning levels to maintain performance with minimal intervention.
A range of features combine to ensure this system provides superior performance when compared to any other slag detection system on the market:
- Increased detection sensitivity near ladle end for slag prevention
- Ongoing tuning adjustments based on historical data
- Plant network connectivity for heat statistics and sensitivity selection
- Real-time system fault and error notifications
- Ladle weight calculator option
Getting Started
Kiss Technologies has been providing the benefits of a ladle slag detection system to our customers for over 20 years. With efficient, successful installations, our KT2000 System is the effective, low-maintenance solution you are looking for. Let’s have a discussion about your process, technical requirements, and economic goals.
Additional Casting Solutions
Importance of Mold Oscillation
M.O.M.S* Technology to Ensure an Optimal Mold/Strand Interface
Achieve product quality, productivity and lower costs with this step-by-step guide. Assure that your mold oscillation mechanism is operating as designed.
Whenever You Need Us,
We're Here For You
You can rely on our unsurpassed products, customer support, problem resolution, and extensive on-site training.
Send us a message
Send us a message
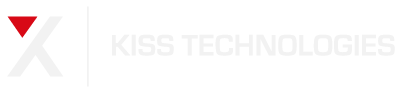
Leading the steel industry for a measurable difference
Providing data-driven insights to continuous casting since 1989. Choose Kiss Technologies for a measurable difference.
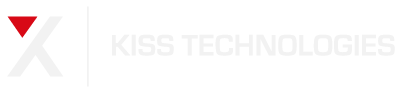
Leading the steel industry for a measurable difference
Providing data-driven insights to continuous casting since 1989. Choose Kiss Technologies for a measurable difference.